Gokhan Gureser
PMP, LSS MBB, ASQ CSSBB
Continuous Improvement Expert
Data Aligning Across Companies and Systems ​
Opportunity
In return and defect product management processes, there were obstacles during information flow. Frequently, company was unable to satisfy customers with a fulfilled response. Since the process involves more than one company, each stakeholder was focused on its own priorities. For instance warehouses had to reach its return product goal, product managers focus on customer satisfaction and suppliers had got defect ppm goals. Hence, this process is not perceived as a long value chain across companies, but as a local problem for each department. Eventually, data handling, visualizing and measurement of the process performance was almost impossible. Moreover, many customer complaints (35%) were disappearing during the process, due to not defining process roles across companies clearly.
​
​
Execution
In this project, prior to creating lean process flow, the whole process’ current state is drawn using Makigami method. All the technical and organizational requirements are collected and elicited. Manual data entry requirements are minimized and a data flow is created.
​
​
Conclusion
Notification system among different stakeholders led fluent process flow among companies and departments. Also, the performance of the system of can be measured any time, by facilitating a reporting and data extraction.
Unattended or negatively resulted customer complaint is reduced from 35% to 5%. Return product cycle time mean is also reduced from 92 days to 29 days. This improvement totally made by DMAIC methodology, as well as business process management practices and requirement engineering tools.

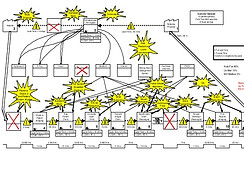