Gokhan Gureser
PMP, LSS MBB, ASQ CSSBB
Continuous Improvement Expert
Overall Equipment Efficiency improvment in batch manufacturing process by SMED
Production capacity is increased and cycle time is reduced using SMED (single minute exchange of dies) method.
The Case and Objective
In pharmaceutical manufacturing process, reducing the compression machine changeover time increases compression capacity.
The objective of the project was to reduce non-value added time including, changeovers, cleaning, shift changes breaks. Therefore, the best-proven approach to accomplish that was SMED single minute exchange of dies used to methodically eliminate waste from the changeover process without sacrificing quality.
The Work
Define
Historical OEE data is collected and feasibility analysis is made to determine whether net value of the project is feasible or not. Main challenge was to maintain cGMP rules and improve the quality.
As can be seen from the figure, it is one of the major opportunities, to reduce OEE (Overall equipment Effectiveness) cycle time.
Measure
Total changeover time is composed of three activities, which can be named as tear down, cleaning and set-up new times. The data is collected classifying times into two and recording the video and determine value added and non-adding activities in each three steps.
Analyze
Most of the lost time was due to searchnn the tools, movements from tool room to the machine room, and searching for documentation papers.
Improve
Improvement opportunities are ordered, brainstorming sessions are arranged to collect as many ideas as possible. Key problems and solutions are:
-
communication problem – Kanban for syncing actions
-
searching for tools – 5S
-
sequential cleaning – simultaneous cleaning
-
documentation time is reduced – simultaneous documentation
Solutions are implemented at a pilot station and then rolled-out to all production operations. The total changeover times is reduced from 32 minutes to 11 minutes. This corresponds for the whole factory to 1.2-day reduction in cycle time and $1,400,000 saving/year.
Control
The solutions are written in both reports format and control procedures and transferred to operations. Therefore, the solution can be maintained for years. SPC tool is used to monitor further situation.
The Result
Solutions are implemented at a pilot station and then rolled-out to all production operations. The total changeover times is reduced from 32 minutes to 11 minutes. This corresponds for the whole factory to 1.2-day reduction in cycle time and $1,400,000 saving/year.
This new method was totally harmonized with cGMP standards. The only discussion in this project was to the decision that whether 5S implementation to tools’ room should be considered as a separate project or not.
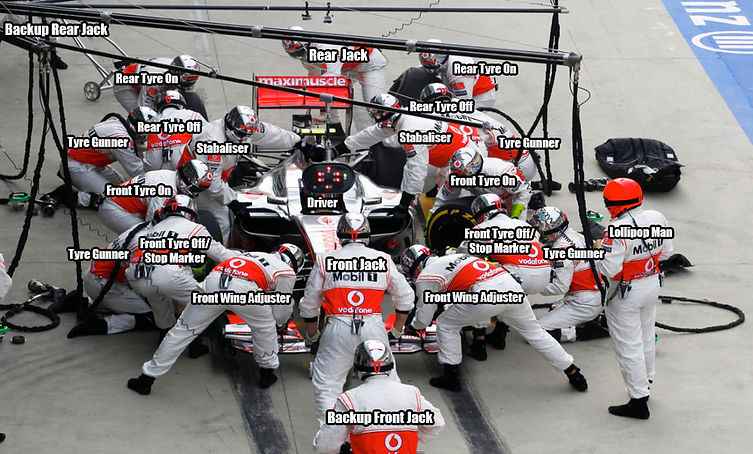